conception. biogas plant.
The dimensioning and design of a biogas plant depend mainly on
- the physical composition and volume of the substrate (the targeted organic waste streams)
- and the type of energies that we want to produce.
location.
Choosing the best location possible for the unit is a very important decision. It differs from case to case, sometimes simple, sometimes difficult with a severe impact on the profitability of the project. The two main criteria are:
- proximity to waste and substrates,
- proximity to the user of energies.
the industrial-scale biogas plant.
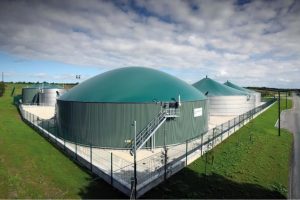
In an industrial/technological installation that decomposes organic matter in the absence of air to produce biogas (i.e. anaerobic digestion) we want to distinguish four different phases :
- Pretreatment processes of feedstock/entrants.
- Fermentation, the actual anaerobic digestion and the biogas production.
- Utilization and preparation of the biogas to produce electricity, heat, steam and fuel.
- Post treatment of digestate.
pretreatment. preparation of inputs / substrates.
Biodegradable waste and substrate vary in terms of energy content, consistency and quantities delivered, they are stored on site, in various tanks and pits.
The different inputs require different pre-treatment methods and grinding techniques (MULTIMix, Rotacut) to ensure the homogeneity and humidification of the substrate which is introduced into the digester, it is also necessary to separate any foreign bodies like stones.
The solid feedin materials are dosed and weighed in a loading / dosing hopper to maintain the recipe, then liquids and water are added, the substrate is inoculated with biomass from the digester.
A programmable pumping unit with automatic valves guarantees the supply of substrate to the digester.
fermentation / digestion process. the actual process inside the digester.
The anaerobic digestion AD process itself takes place inside the tank / digester. This process of fermentation or biodigestion is ensured by the action of certain interacting microbial groups. It takes place in 4 stages. Each step involves a different type or set of bacteria; the stages overlap and ideally the families of bacteria coexist in harmony inside the fermentation tank (digester) in order to ensure a stable process and a high rate of biogas production. The four phases are hydrolysis, acidogenesis, acetogenesis and methanogenesis.
In order to assure an overall stable anaerobic digestion process with a high methane yield and according to expectations, it is essential that the distinct but overlapping microbial conversion stages go hand in hand with one another, to avoid non-desired intermediary substances. The different bacteria families adapt slowly to one another, once the equilibrium is found any external shock shall be avoided as it may have catastrophic consequences to the little universe inside the digester: Inhibition.
It is biological stability which is essential in AD and guarantees good biogas production, all parameters such as feed stock recipe, temperature and pH-value should be kept constant to avoid disruptions and the accumulation of undesirable intermediate substances.
biogas. utilization.
The biogas constituents are respectively 50% -60% of methane CH4 and 35% -45% of carbon dioxide CO2. It also contains water vapor and gases such as hydrogen H2, hydrogen sulfide H2S, O2, CO, other contaminants. Before recovery, the biogas is subjected to one or more cleaning and refining processes.
desulfurization.
Hydrogen sulfide H2S is formed in the digester all the time. The H2S load depends mainly on the substrates / inputs. In wastewater treatment plants, or waste treatment units. The H2S concentration can reach 2000 to 3500 ppm, installations that process paper pulp or vinasse for ethanol production can see even higher concentrations up to 15,000 ppm and more.
H2S is a flammable, very corrosive gas, with the foul smell of rotten egg and very toxic. Hydrogen sulfide destroys equipment and especially internal combustion gas engines. It also is much less of a nuisance and danger to human health and the environment if treated properly.
Desulfurization takes place in several steps, and comprises all the devices/reactors/filters and measures that are taken:
- inside the digester, though the injection of air,
- inside the digester, by introduction iron hydroxide,
- after the digestion, by means of a biological reactor (trickling filter), mainly to remove large H2S loads and desulfurize down to 200 ppm. generizon is associated with TS-Umweltanlagenbau, in Germany, with several installations in Morocco in operation.
- through a chemical reactor to remove large loads of H2S and desulfurize down to 200 ppm. generizon can deliver several solutions with several suppliers.
The biological process can be considered cheaper, without operating costs for the chemical. The chemical process has its justification for start / stop applications in the event of sudden increases in H2S. - The last stage finalizes the desulfurization by means of an activated carbon filter which polishes up down to at less than 20 ppm.
utilization. energy use.
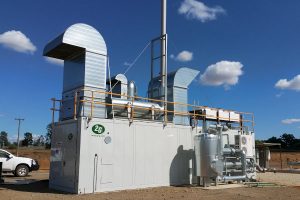
Subsequently the biogas can be utilized
- directly in a boiler for the production of steam,
- in a gas2power g2p engine, for the production of electricity only.
- in a combined heat and power biogas engine for
- electricity and heat (hot water).
- electricity, heat (hot water), and steam (with steam generator).
- electricity, steam and hot air.
- trigeneration: production of electricity, heat / steam and air conditioning.
upgrading. purification. gas separation. bio-methane.
Biogas can be upgraded to bio-methane through the separation of gases, in particular methane and carbon dioxide. Separation / upgrading is done by a compressor and membrane technology, the resulting bio-methane has a purity of up to 99.5% CH4, the quality of natural gas. generizon can supply the complete unit preinstalled in a container.
The bio-methane is eventually used as:
- fuel for vehicles or trucks; green mobility,
- compressed natural gas CNG: compressed bio-methane for transport or storage,
- liquefied natural gas LNG: bio-methane liquefied at cryogenic temperatures (-260 ° C), for transport or storage.
generizon can provide the bio-methane storage station as well as the service station for trucks, buses and natural gas powered vehicles NGV.
production of industrial CO2.
In the gas separation process, it is possible to capture the residual gas, carbon dioxide CO2. After a few additional downstream purification washing steps the carbon dioxide, may be utilized:
- in crop greenhouses to accelerate the photosynthesis,
- in the production of algae or other biomass in a photobioreactor,
- or used in the food and beverages industry.
residue / digestate. post treatment.
The digestate is the residue of the anaerobic digestion process: It is organic matter which is more or less completely degraded / mineralized, the organic part of the substrate which is indigestible like lignocellulose matter, and dead bacteria, mineralized. 85% to 90% of the initial substrate remains on the exit from the digester; the digestate represents a high-quality bio-fertilizer.
The digestate, rich in nutrients (NPK), is largely utilized as is, as a fertilizer. It can also be separated in a liquid and a solid phase; convert respectively to a liquid mineral fertilizer and to a solid organic soil amendment.
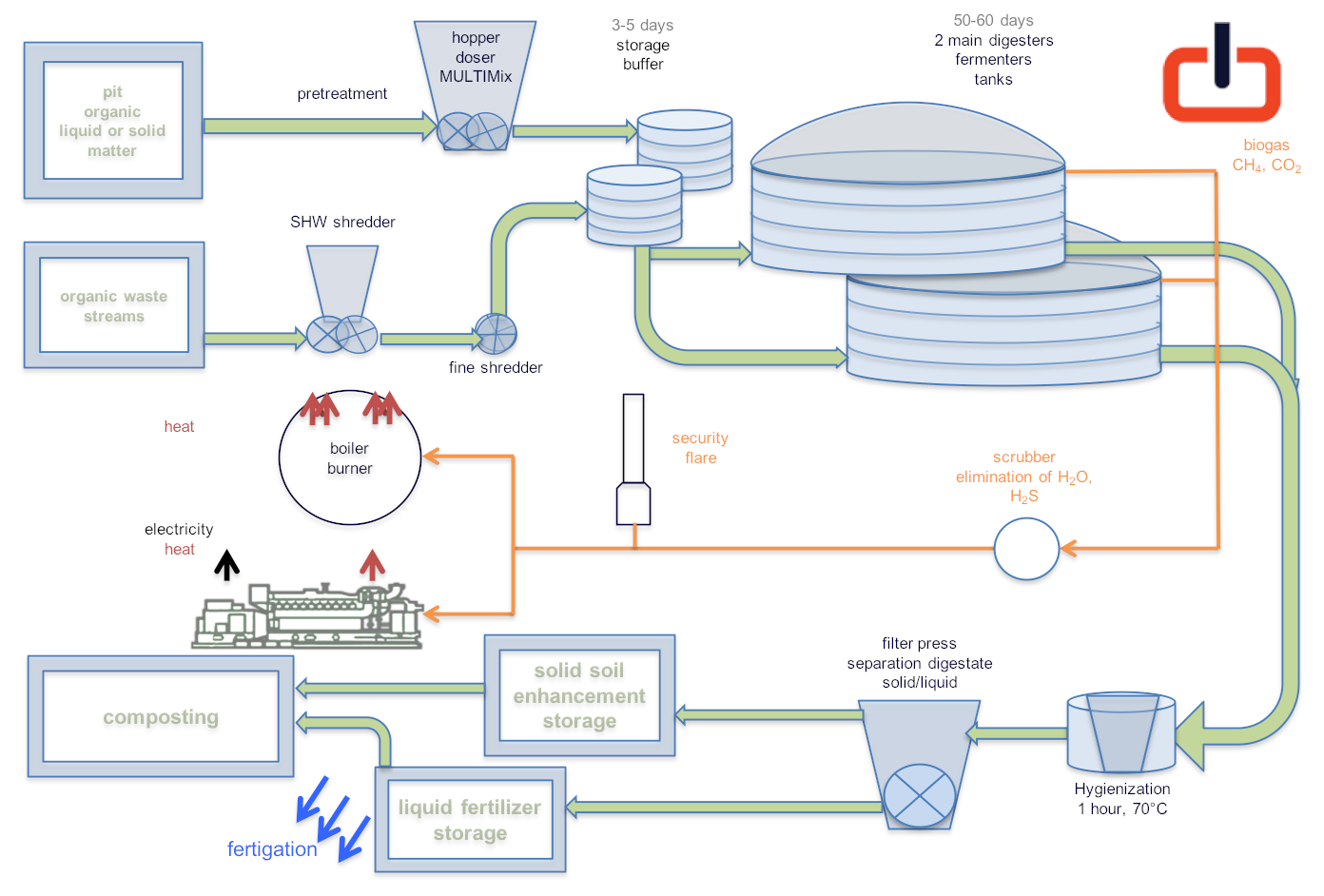